Técnica que se utiliza en el diseño y la construcción de robots y aparatos que realizan operaciones o trabajos, generalmente en instalaciones industriales y en sustitución de la mano de obra humana.
"las comunicaciones, la informática, la robótica y todas las aplicaciones de la electrónica en general tienen su origen en la electricidad y el magnetismo"¿QUÉ ES UN ROBOT? ¿CUÁL ES EL ORIGEN DE LA PALABRA ROBOT?
Robot, máquina controlada por un ordenador y programada para moverse, manipular objetos y realizar trabajos a la vez que interacciona con su entorno.
Los robots son capaces de realizar tareas repetitivas de forma más rápida, barata y precisa que los seres humanos. El término procede de la palabra checa robota, que significa “trabajo obligatorio”; fue empleado por primera vez en la obra teatral de 1921 R.U.R (Robots Universales de Rossum) por el novelista y dramaturgo checo Karel Éapek. Desde entonces se ha empleado la palabra robot para referirse a una máquina que realiza trabajos para ayudar a las personas o efectúa tareas difíciles o desagradables para los humanos.
HISTORIA DE LA EVOLUCIÓN DE LOS ROBOTS
El concepto de máquinas automatizadas se remota a la antigüedad, con mitos de seres mecánicos vivientes. Los autómatas, o máquinas semejantes a personas, ya aparecían en los relojes de las iglesias medievales, y los relojeros del siglo XVIII eran famosos por sus ingeniosas criaturas mecánicas. Algunos de los primeros robots empleaban mecanismos de realimentación para corregir errores, mecanismos que siguen empleándose actualmente. Un ejemplo de control por realimentación es un bebedero que emplea un flotador para determinar el nivel del agua. Cuando el agua cae por debajo de un nivel determinado, el flotador baja, abre la válvula y deja entrar más agua en el bebedero. Al subir el agua el flotador también sube, y al llegar a cierta altura se cierra la válvula y se corta el paso del agua. El primer auténtico controlador realimentado fue el regulador de Watt, inventado en 1788 por el ingeniero británico James Watt. Este dispositivo constaba de dos bolas metálicas unidas al eje motor de una máquina de vapor y conectadas con una válvula que regulaba el flujo de vapor. A medida que aumentaba la velocidad de la máquina de vapor, las bolas se alejaban del eje debido a la fuerza centrífuga, con lo que cerraban la válvula. Esto hacía que disminuyera el flujo de vapor a la máquina y por tanto la velocidad. El control por realimentación, el desarrollo de herramientas especializadas y la división del trabajo en tareas más pequeñas que pudieran realizar obreros o máquinas fueron ingredientes esenciales en la automatización de las fábricas en el siglo XVIII. A medida que mejoraba la tecnología se desarrollaron máquinas especializadas para tareas como poner tapones a las botellas o verter caucho líquido en moldes para neumáticos. Sin embargo, ninguna de estas máquinas tenía la versatilidad del brazo humano, y no podían alcanzar objetos alejados y colocarlos en la posición deseada. El desarrollo del brazo artificial multiarticulado, o manipulador, llevó al moderno robot. El inventor estadounidense George Devol desarrolló en 1954 un brazo primitivo que se podía programar para realizar tareas específicas. En la década de 1970 los robots se difundieron en muchos otros sectores industriales, desde la industria mecánica a la electrónica, tanto así que ya se emplean en las más variadas tareas, sueldan y pintan automóviles, embalan materiales y objetos, alzan pesadas cargas, atornillan y desatornillan tuercas, sueldan circuitos. En 1975, el ingeniero mecánico estadounidense Victor Scheinman, cuando estudiaba la carrera en la Universidad de Stanford, en California, desarrolló un manipulador polivalente realmente flexible conocido como Brazo Manipulador Universal Programable (PUMA, siglas en inglés). El PUMA era capaz de mover un objeto y colocarlo en cualquier orientación en un lugar deseado que estuviera a su alcance. El concepto básico multiarticulado del PUMA es la base de la mayoría de los robots actuales. La investigación en este campo ha dado pasos de gigante en los últimos años, ya que se están trabajando en robots, para emplearlos en asistencia a minusválidos, en intervenciones de los primeros auxilios en lugares inaccesibles o en la eventualidad de catástrofes ambientales. Este último es el caso de la telerrobótica, sector de investigación nacido en los últimos años con el objeto de estudiar y desarrollar robots que puedan ser controlados a distancia. De todos modos, ya en 1979, en Estados Unidos, tras el accidente nuclear de Three Mile Island se utilizaron robots para retirar los desechos radiactivos.
¿CÓMO FUNCIONAN LOS ROBOTS?
El diseño de un manipulador robótico se inspira en el brazo humano, aunque con algunas diferencias. Por ejemplo, un brazo robótico puede extenderse telescópicamente, es decir deslizando unas secciones cilíndricas dentro de otras para alargar el brazo. También pueden construirse brazos robóticos de forma que puedan doblarse como la trompa de un elefante. Las pinzas están diseñadas para imitar la función y estructura de la mano humana. Muchos robots están equipados con pinzas especializadas para agarrar dispositivos concretos, como una gradilla de tubos de ensayo o un soldador de arco. Las articulaciones de un brazo robótico suelen moverse mediante motores eléctricos. En la mayoría de los robots, la pinza se mueve de una posición a otra cambiando su orientación. Una computadora calcula los ángulos de articulación necesarios para llevar la pinza a la posición deseada, un proceso conocido como cinemática inversa. Algunos brazos multiarticulados están equipados con servo controladores o controladores por realimentación que reciben datos de un ordenador. Cada articulación del brazo tiene un dispositivo que mide su ángulo y envía ese dato al controlador. Si el ángulo real del brazo no es igual al ángulo calculado para la posición deseada, el servo controlador mueve la articulación hasta que el ángulo del brazo coincida con el ángulo calculado. Los controladores y los ordenadores asociados también deben procesar los datos recogidos por cámaras que localizan los objetos que se van a agarrar o las informaciones de sensores situados en las pinzas que regulan la fuerza de agarre.
Cualquier robot diseñado para moverse en un entorno no estructurado o desconocido necesita múltiples sensores y controles (por ejemplo, sensores ultrasónicos o infrarrojos) para evitar los obstáculos. Los robots como los vehículos planetarios de la NASA necesitan una gran cantidad de sensores y unas computadoras de a bordo muy potentes para procesar la compleja información que les permite moverse. Eso es particularmente cierto para robots diseñados para trabajar en estrecha proximidad de seres humanos, como robots que ayuden a personas discapacitadas o sirvan comidas en un hospital. La seguridad debe ser esencial en el diseño de robots para el servicio humano.
Elementos Constitutivos de un Robot Industrial
- Manipulador o brazo mecánico,
- Elementos motrices o actuadores,
- Controlador,
- Efector terminal. Herramienta o aprehensor,
- Sensores de información en los robots inteligentes.
- Cuales son las partes de un robot
- La estructura
Los mecanismos
Son los elementos que permiten transmitir el movimiento entre sus partes. Los movimientos de giro, de desplazamiento.
Por ejemplo los engranajes, las poleas, las correas, las ruedas, etc.
Las fuentes de energía
Aquí podemos distinguir la energía eléctrica, que en nuestro caso serán las baterías, y la energía mecánica, que es entregada al robot por el motor.
El motor convierte energía eléctrica en energía mecánica
Los elementos de control:
Son los elementos que permiten controlar las acciones del robot, existen diferentes modelos.
El nuestro es el ladrillo NXT
Los sensores:
Son lo elementos que le entregan información al robot para que éste pueda conocer la situación exterior.
Por ejemplo sensores de tacto, de luz, de temperatura, etc.
La programación:
El programa (software) le indica al elemento de control que debe hacer. Existen varios lenguajes de programación.
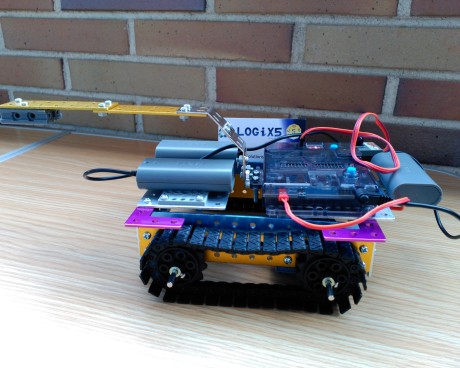
Las ventas globales de robots corroboran esta idea. Según el Reporte Mundial de Robótica de 2018 de la International Federation of Robotics, un número récord de 381,000 robots fueron enviados alrededor del mundo en 2017, un incremento del 30 por ciento comparado con 2016. Para 2018, ese número se espera incrementar en un 10 por ciento hasta 421,000 robots.
La maduración del mercado de los robots de manufactura llega en un tiempo oportuno tanto para talleres grandes como pequeños. La falta de mano de obra capacitada y la dificultad de atraer gente joven a este campo hace atractiva la atención automatizada de máquinas, especialmente para talleres que buscan incrementar la utilización de husillo y operar de manera desatendida durante la noche. Los robots también pueden ayudar a atraer nuevas contrataciones de personas que no se limitan a cargar y descargar máquinas durante todo el turno.
Los robots fueron particularmente notables en la Feria Internacional de Máquinas-Herramienta de Japón (JIMTOF) el pasado noviembre, la cual fue la edición 29 de la exhibición bienal organizada por la Asociación de Fabricantes de Máquinas-Herramienta de Japón y que tuvo lugar en el centro de convenciones Tokyo Big Sight. Al igual que en el International Manufacturing Technology Show (IMTS) el pasado mes de septiembre en Chicago, Illinois, la JIMTOF 2018 batió récords previos de visitantes (más de 153,000 este año) y número de expositores (1,085). El interés de la industria en exposiciones como estas ciertamente no está disminuyendo, ya que los fabricantes continúan visitándolas para aprender cómo las estrategias de talleres, como la automatización, pueden incrementar la eficiencia de sus negocios e impulsar el crecimiento.
Expectativas, ejemplos de evolución
Aquí se presentan tres expectativas que creo que los talleres tienen sobre los robots. Estos puntos se ilustran con ejemplos que vi en la exposición de cómo la tecnología ha evolucionado con respecto a cada expectativa:
1. Los robots deberían ser capaces de operar de forma segura al lado de las personas.
Los fabricantes continúan necesitando robots convencionales con protecciones de seguridad para evitar que la gente ingrese al área de trabajo de los robots, especialmente cuando las aplicaciones piden alta velocidad o capacidad de carga útil. Sin embargo, en JIMTOF hubo muchos (si no más) robots colaborativos o “cobots” en exhibición.
Los cobots usan tecnología de detección para evitar lastimar a las personas en una misma área de trabajo. En algunos casos, los sensores se integran en el robot mismo para detener su movimiento cuando inesperadamente hace contacto con un objeto o una persona. Otra aplicación usa sensores para disminuir o parar el movimiento del robot, según sea la proximidad de una persona al área de trabajo.
Cuando los cobots eran nuevos en la escena de la automatización, los estándares ISO 10218 existentes sobre requerimientos de seguridad de robots industriales (publicada en 2011) no atendían adecuadamente su integración segura en unas instalaciones de manufactura. Esto motivó a la comunidad de automatización a desarrollar la especificación técnica ISO/TS 15066. Un aspecto importante de esto es que da guía a los integradores de robots y al personal de manufactura sobre cómo adelantar evaluaciones de riesgo preliminares más sofisticadas, tanto del cobot como del ambiente que compartirá con los humanos.
Otra señal de que el interés en el cobot está incrementando es el desarrollo de efectores finales diseñados específicamente para ellos. Un ejemplo en la exhibición fue la pinza Co-act de Schunk, la cual ofrece una cubierta suave y carece de esquinas agudas y puntos punzantes. La fuerza de agarre también es menor a 140 Newtons (según ISO/TS 15066) para evitar lesiones.
2. Los robots deberían ser capaces de ser redesplegados a múltiples máquinas en una instalación.
Los talleres de trabajos o subcontratación que mecanizan una alta mezcla de partes en bajos volúmenes pueden beneficiarse de la carga robótica, así como pueden hacerlo las operaciones de alta producción. Las unidades de carga móviles y auto-contenidas con robots o sistemas de recolección de partes pueden facilitar esto. Una vez el trabajo se completa en una máquina, la unidad puede moverse fácilmente a otra con un gato de palets o un elevador. Unos niveladores alinean estas unidades con la máquina. Algunas unidades trabajan con varios controles de máquinas-herramienta y no requieren que el fabricante de máquinas-herramienta suministre una interfaz de robot especial. En cambio, un controlador lógico programable (PLC) es todo lo que se necesita para conectar la máquina y el cargador.
En JIMTOF, unos pocos fabricantes de máquinas-herramienta llevaron esto un paso más allá al integrar cobots con vehículos guiados automatizados (AGVs) que pueden moverse autónomamente de máquina a máquina. Los AGVs usan tecnología de detección para guiarlos con seguridad a través de una instalación sin golpear equipos o personas mientras se redespliegan a otro equipo.
3. Los robots deberían ser fáciles de integrar.
El ejemplo arriba describe cuán fácil puede ser integrar un robot con una máquina-herramienta. Sin embargo, estos casos se demostraron más claramente en los stands de fabricantes de máquinas-herramienta sin ningún robot en exhibición. El mensaje no es que los robots no sean importantes o valiosos, sino que la integración es tan fácil que los fabricantes de máquinas-herramienta no consideran que los robots sean una parte necesaria de un stand de una feria.
Dicho esto, algunas máquinas-herramienta tienen automatización robótica incorporada, de modo que un integrador no es necesario. Por ejemplo, Murata mostró unos tornos con plato de doble husillo y cargadores gantry integrados. De hecho, la compañía ahora ofrece cargadores gantry de fibra de carbono que se moverán hasta 50 por ciento más rápido que los cargadores estándar.
Además, Okuma introdujo el torno CNC LB3000 EX con Armroid, un cargador de robot articulado que se monta en el área de trabajo de la máquina para carga/descarga de partes. El sistema operativo del robot no requiere aprendizaje durante nuevos alistamientos de trabajo, y puede realizar movimientos sin colisiones mientras se realiza el mecanizado de una parte. El robot puede almacenar tres efectores finales diferentes y cambiarlos según sea necesario de acuerdo con la aplicación. Como en el ejemplo anterior, integrar el robot en la máquina conserva espacio en el piso./s3.amazonaws.com/arc-wordpress-client-uploads/infobae-wp/wp-content/uploads/2017/11/07174235/Aibo-perro-robot-2.jpeg)
/s3.amazonaws.com/arc-wordpress-client-uploads/infobae-wp/wp-content/uploads/2017/11/07174235/Aibo-perro-robot-2.jpeg)
El ser humano se siente amenazado por el avance de los robots, aquellos que le "robarían" su trabajo en un futuro cercano. "Esto es el capitalismo, después de todo, y la automatización es inevitable", escribe el escritor Matt Simon en un artículo de la revista Wired.
Sin embargo, destaca que es más probable que trabajemos junto a robots antes de ser reemplazados. Además, Simon asegura que en algunos años, las personas podremos entablar algún tipo de amistad con ellos. Y lejos quedará la idea de ser asesinados por un androide, al menos, fuera de la ficción.
En efecto, la palabra robot surgió en 1921, en la obra de teatro de ciencia ficción "R.U.R.", del checo Karel Capek. Allí, los robots parecían humanos, no estaban hechos de metal, sino de pasta química, y eran asesinos.
Décadas después, películas como "Terminator" o "Blade Runner", entre tantas, seguirían sosteniendo esta idea.
/s3.amazonaws.com/arc-wordpress-client-uploads/infobae-wp/wp-content/uploads/2017/07/28095332/terminator.jpg)
Simon señala que hoy la definición real de robot aun no es clara. "Si se les preguntara a 10 expertos sobre ello, obtendríamos 10 respuestas distintas", asegura.
Sin embargo, hay algunas pautas generales: un robot es una máquina inteligente, que puede realizar tareas de forma autónoma, y logra manipular su entorno.
El futuro del trabajo
Existen estimaciones con respecto a la cantidad de trabajos que desaparecerán con la llegada de los robots y la IA (inteligencia artificial). En su informe "Future of Jobs 2018" (el futuro de los trabajos), el Foro Económico Mundial (WEF, por sus siglas en inglés) pronostica que se perderán empleos.
Hoy el 29% de las tareas laborales son realizadas por una máquina. Este porcentaje significaría la pérdida de 75 millones de empleos en 2025, debido a los avances tecnológicos.
Sin embargo, el WEF señala que se crearán nuevos roles o funciones que necesitarán de un mayor grado de especialización. Así, se abrirán oportunidades que permitirán el surgimiento de más de 133 millones nuevos roles de trabajo.
Tareas 3D
"La IA está en pleno desarrollo. Abarca las áreas de visión artificial, procesamiento de habla y aprendizaje automático. Estas herramientas se están empezando a aplicar en áreas como economía, medicina, arte y más", señala a Infobae la Dra Marcela Riccillo, especialista en IA y robótica.
Continúa: "Los robots y los sistemas con técnicas de IA son herramientas que podrían ayudar a los humanos en tareas que son las llamadas 3D en inglés: tareas dangerous (peligrosas), dirty (sucias) y dull (tediosas)".
"En general, en estos temas se están desarrollando, por ejemplo, los smart speakers (parlantes inteligentes), los vehículos autónomos (donde ya hay pruebas con taxis robots) y humanoides como Pepper de SoftBank", finaliza.
¿Cuáles son los 5 robots más destacados de 2018 y por qué?
1- Pepper
Es un robot semi-humanoide fabricado por SoftBank Robotics (desarrolladdo originalmente por la francesa Aldebaran Robotics). Es una compañía que preside Masayoshi Son, el segundo hombre más rico de Japón.
Pepper fue presentado en 2014 y en 2015 ya se vendía en el país nipón. Desde la compañía, dicen que es el primer robot humanoide social del mundo. Puede reconocer rostros y emociones humanas básicas.
Desde SoftBank impulsan hoy el crecimiento de Pepper en Occidente, con una fuerte presencia en Estados Unidos. Actualmente, el robot está presente en empresas y escuelas.
Por ejemplo, más de 2.000 compañías ya lo adoptaron como asistente para recibir, informar y guiar a los visitantes que reciben. ¿Cómo ha crecido Pepper en América en 2018?
"Se ha convertido en un recurso instrumental para las empresas en los Estados Unidos. Ha mejorado su capacidad para aprender, evolucionar y adoptar nuevas características. Continúa comprometiendo e informando a los clientes, capacitando a los empleados, optimizando las operaciones y facilitando el aprendizaje", responde a Infobae Steve Carlin, Director de Estrategia de SoftBank Robotics América.
/s3.amazonaws.com/arc-wordpress-client-uploads/infobae-wp/wp-content/uploads/2018/12/19102645/Steve-Carlin-Softbank-en-America-1920-2.jpg)
Respecto de los planes a futuro, Carlin explica que Pepper trabajará con una nueva plataforma en América a partir de principios de 2019. "Esta plataforma permitirá un desarrollo y una mejora más rápidos, que ofrece más control y escalabilidad para los clientes", dice.
Continúa: "La nueva plataforma basada en la nube de Pepper maximizará su potencial como un dispositivo de vanguardia dentro del ecosistema de IoT -internet de las cosas- de cualquier empresa".
En este sentido, según señala el ejecutivo, el objetivo es que Pepper pueda conectarse a las herramientas de una empresa (sistemas de gestión de inventario, por ejemplo). Así, recibirá información y análisis en tiempo real, que irá procesando.
En cuanto al futuro el trabajo, el representante de SoftBank se muestra optimista: "La IA jugará un papel importante en la fuerza laboral del futuro. La próxima generación de robots no está trabajando para reemplazar a las personas, sino en mejorar sus vidas y sus trabajos".
2- Atlas
Es el robot de los virales por excelencia y ha evolucionado en sus habilidades notoriamente durante 2018. Desarrollado por la compañía de Estados Unidos Boston Dynamics, se dio a conocer en 2013.
El robot mide 1.50 metros y pesa 75 kilogramos, fue diseñado para tareas de búsqueda y rescate. Puede correr a gran velocidad, saltar obstáculos y hasta hacer parkour (es una actividad física, algo así como una "acrobacia urbana").
"Sin duda, Atlas es el robot del año. Sigue siendo el robot humanoide más sofisticado por lejos. El video del robot haciendo parkour, tomando decisiones completamente autónomas para navegar un espacio tan irregular es una muestra clara de su extraordinario avance", señala a Infobae el emprendedor y tecnólogo Santiago Bilinkis.
En el video viral del parkour, se ve a Atlas saltando obstáculos de 40 cm de altura, de forma dinámica, cambiando su peso de su pie derecho a su pie izquierdo. Movimientos hipnóticos, oro para internet.
3-Insight
"El InSight es el robot geofísico que lanzó NASA en mayo de este año y llegó a Marte el 26 de noviembre de 2018. Tiene sensores que miden el suelo y la temperatura para analizar la evolución geológica del planeta", expresa a Infobae Mateo Salvatto, joven emprendedor argentino, creador de de la app Háblalo y campeón internacional de robótica.
Continúa: "La tecnología de InSight permite entender mejor los planetas similares (Venus, Mercurio y etc). En resumen estudia la estructura interna del planeta. Lo considero el robot del año".
InSight comenzó siendo una nave y se convirtió en un robot complejo, el primero en posarse en Marte e investigarlo. Desde su aterrizaje, estuvo enviando fotos y sonidos del planeta.
"Hubo muchos robots piolas este año pero éste es un aporte grande a la exploración espacial y todo lo que nos aporte de info sobre Marte hace más posible el viaje allá que se planea en 2030. Es importantísimo", concluye Salvatto.
No hay comentarios:
Publicar un comentario